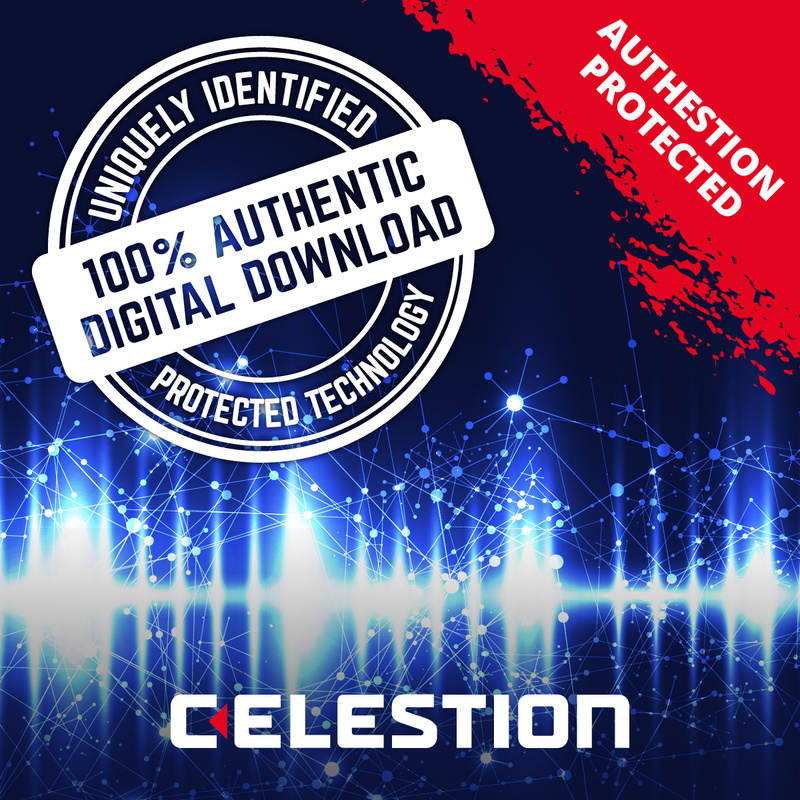
Ipswich, UK (August 1, 2017) — After customer requests for more information, Celestion is pleased to share insights into the technology behind Authestion Marked, their own proprietary audio protection technology for their digitally downloadable catalog of Impulse Responses. This technology is designed both to reassure customers they have purchased genuine Celestion brand downloads and to track unauthorized sharing of the downloads. The company has Authestion Marked the full range of authentic Celestion Impulse Responses available at Celestion Plus.
Authestion Marked technology represents a marked improvement over traditional digital marking of audio files for music to ensure authorized use. The audio engineers at Celestion developed this special technology to meet the unique characteristics of downloadable Impulse Response files –without any effect on the way that the genuine tones sound. Authestion is essentially audibly invisible – so customers can be assured that Celestion IRs always represent the definitive digital representations of the company’s classic guitar speaker tones.
When a customer places an order for a particular Celestion IR download, Authestion works by adding a unique Identifier within the waveform of the file, making it unique and therefore traceable. The Identifier does not capture any personal data of the customer, nor effect the way the IRs work or are installed by the licensed user. This simply allows Celestion to determine when and who purchased the IR file and track the use of the downloads should unauthorized, widespread sharing be encountered.
“Celestion has invested a great deal in developing and perfecting our genuine Impulse Responses, using the finest state-of-the art gear, award-winning engineers and world-class recording facilities,” says Nigel Wood, Celestion Managing Director. “Having our authentic IR downloads Authestion Marked is not only important to us, given the expertise and efforts we’ve put into such a high quality product, but also fair to our valued customers who have paid to download authentic Celestion IRs.”
View the complete range of Authestion Marked Celestion Impulse Responses available at Celestion Plus, including the A-Type, Neo Creamback, G12-H150 Redback, G12M Greenback, G12M-65 Creamback, G12M-75 Creamback, G12H Anniversary, G12-65, Celestion Blue and Vintage 30 models mounted in 1×12 and 2×12 open and closed back and 4×12 cabinets (5 varieties of each.) All the Celestion IRs are available for download both as an individual single cabinet-type IR as well as a full collection.
Read more about Authestion Marked technology on the Celestion Plus blog: https://www.celestionplus.com/news/authestion-marked-celestion-impulse-response-downloads/.
About Celestion Impulse Responses
Celestion IRs, which capture the essential behavior of the cabinet in the specific space in which it was recorded, including the frequency and phase response of single drivers as well as the interaction of multiple speakers, offer the user significant benefits. In both recording and live production, Celestion IRs enable the desired tone to be precisely and consistently reproduced regardless of the music recording or live sound environment. And IR users can escape the limitations of a single mic and cabinet setup and explore a universe of possibilities to create the perfect tone. Once you find a tone that you love, it can be precisely recreated, in the studio or on the road, time after time. And the IRs allow Celestion customers to audition specific models before purchasing one or more physical speakers.
Celestion IR digital downloads are available in uncompressed, industry standard .WAV format at 44.1 kHz, 48 kHz, 88.2 kHz and 96 kHz sample rates at 24 bit depth, in lengths of 200 and 500 milliseconds Once the files are downloaded and unzipped, users simply load the IRs into a convolution plug-in in their DAW or into other processing hardware. These formats will work in all known hardware capable of loading IRs, and for the most popular hardware Celestion have already grouped together the correct formats. Guitar processor manufacturers supported include Atomic Amps, Fractal Audio Systems, Kemper, Line 6, Logidy, Positive Grid, Two Notes, Headrush and Yamaha. The Celestion IR files may be downloaded in the sample rate and length appropriate for the hardware being used or as a complete package of all rates and lengths. Certain third party hardware requires the files to be converted into a proprietary format before use. Visit Celestion Plus.
About Celestion and Celestion Guitar Speakers
An important element to essential British guitar tone since the birth of Rock & Roll, Celestion Guitar Speakers are famous for their lively and vocal midrange character with plenty of sparkle and chime. With worldwide headquarters in Ipswich, England, Celestion design, develop and manufacture premium guitar and bass loudspeakers, and high-quality professional audio drivers for sound reinforcement. These world-renowned speakers are used onstage and in clubs, theatres and other venues the world over. Contact Celestion at: info@Celestion.com and visit us on Facebook at www.Facebook.com/Celestion.
www.celestion.com